About Modern Engineering
Designing and manufacturing high-quality machines since 1995
Modern Engineering Company is since 1995 in this field, MODERN ENGINEERING CO. designs and manufactures machines for all the processes of the Paint, Ink, Adhesive, Construction Chemicals, Dye, Pigment industry, Ceramic industries and Resin in industry, Modern Engineering CO. is the only indigenous company that provides an end to end solution to those companies/individuals who intend to setup a complete plant.
Modern Engineering Company is the leading manufacturers and exporters of Machinery for the manufacture of products like Sand mill, Hydraulic disperser, High speed disperser, low speed disperser, Resin plants, All type of blender, Sigma mixer(Kneader) and a range of other products.
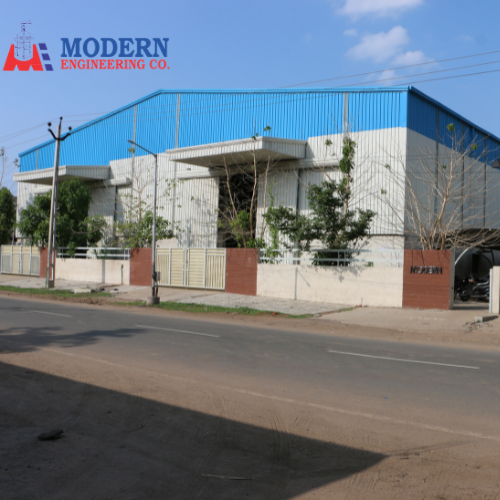
Why Choose Us?
We combine expertise, quality manufacturing, and innovative solutions to deliver exceptional industrial machinery
Our Clients
Trusted by leading companies across various industries